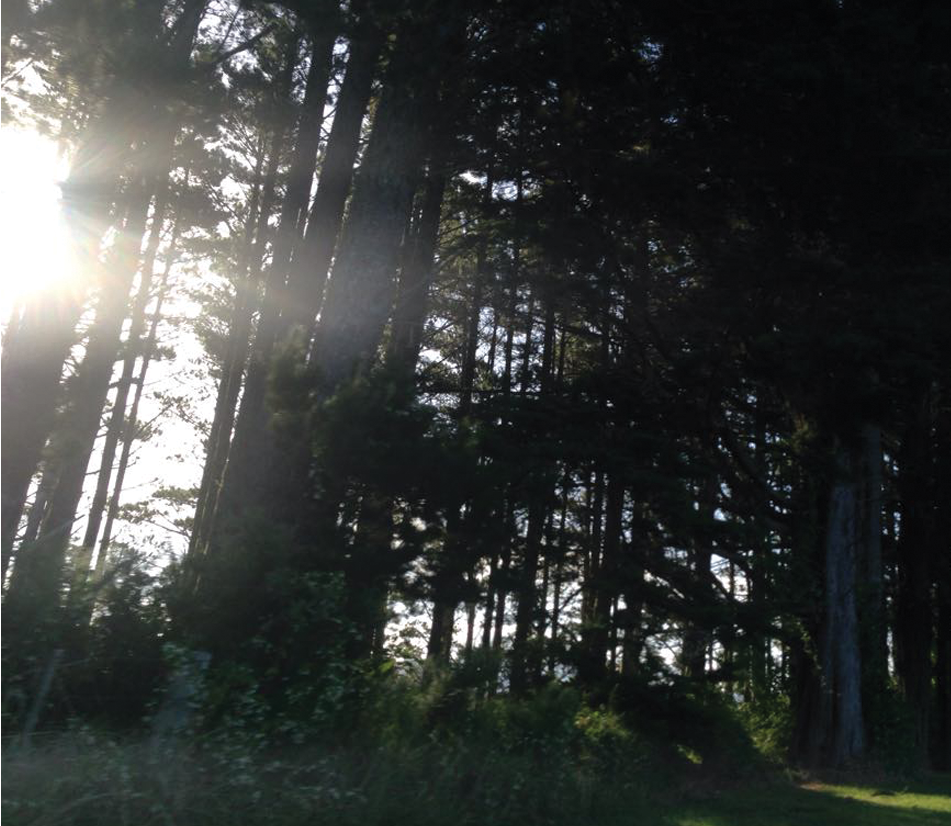
The Woodtex® Panel starts life as the center core of the pine tree, a grade of wood that is not used for timber framing. These cut cores are kiln dried and cut into blocks 500mm at the Woodtex® factory. Then are stacked for air drying.
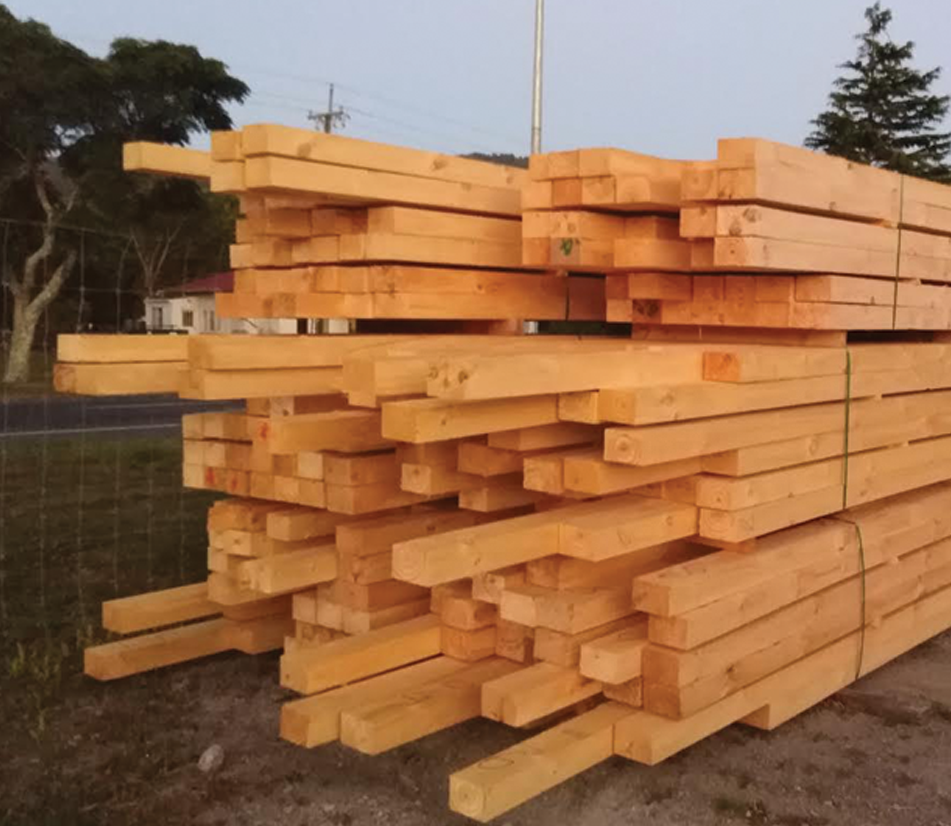
In production, the blocks are grated into wood wool that travels up a conveyor to be sprayed with water and mixed with Portland cement, tumbled and massaged so that every strand is coated in Portland cement.
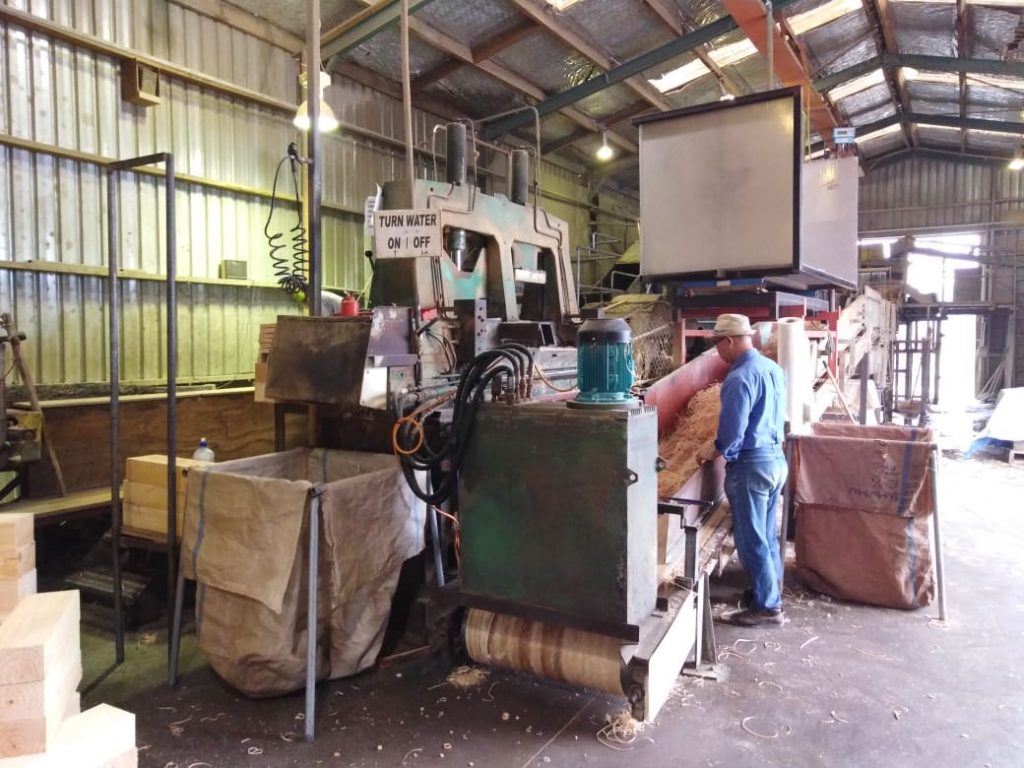
As the wood wool cement mixture is passed along the conveyor it arrives at the form platform where the mixture is cut and pressed into the forms that turn it into Woodtex® Panels.
The Woodtex® Panels are held under compression for 48 hours before being turned out where it is filleted and stacked for 21 days to complete the cure stage.
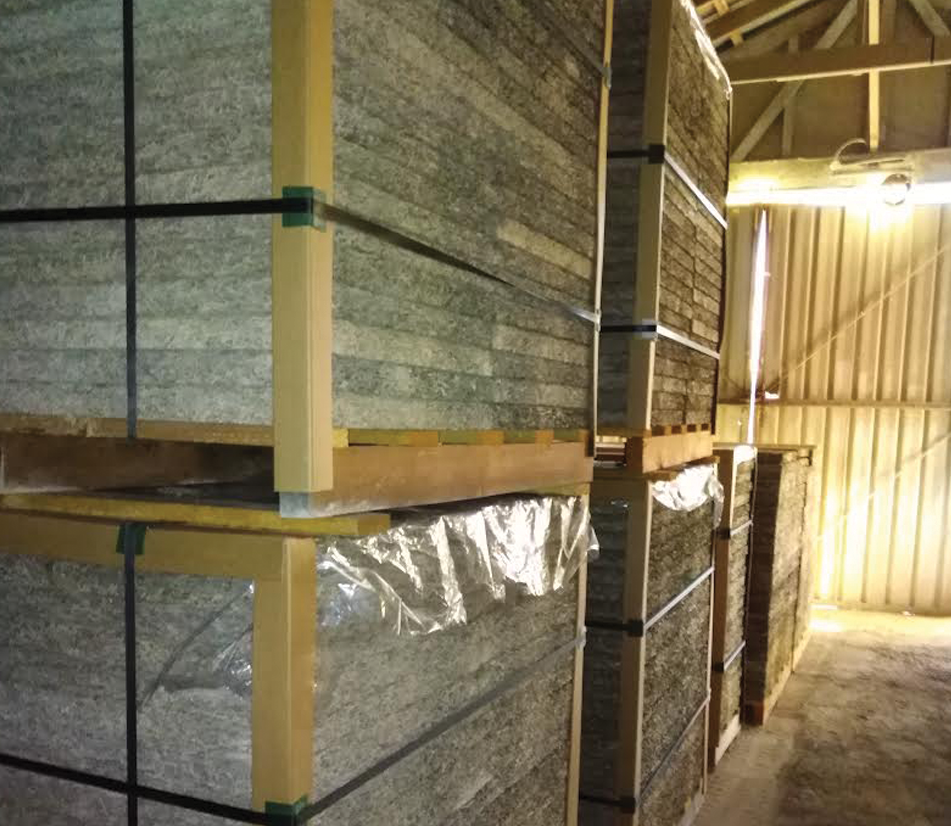
As orders are received the Woodtex® Panel is then cut and trimmed as required. Every strand of the wood wool is now “petrified” in the Portland cement and bound as a mass to create the panel, this gives the Woodtex® Panel the quality of being resilient against
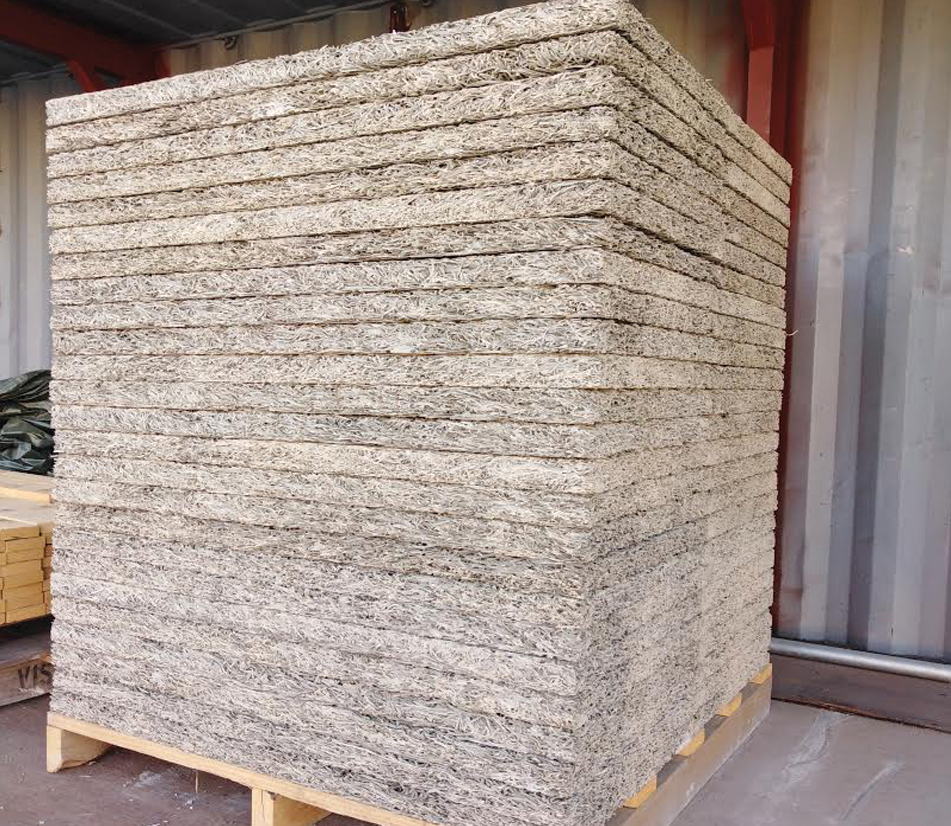